INDUCTION FURNACES
MARX has been active in the foundry industry for more than 60 years. Almost every furnace brand has been serviced, repaired, technically upgraded or newly built in our company. With this experience, we are able to offer holistic solutions for our customers - starting with engineering and new production, through modernization and retrofitting of induction systems to comprehensive service and customer service.
With our locations in Iserlohn, Hennigsdorf and Donauwörth, we are there for you - in an emergency 24 hours a day at our emergency number +49 (0) 172-2799564.
Hatim Britechi Sales Iserlohn
Tel.: +49 (0)2371 - 2105 - 34
E-Mail: britechi@marx-gmbh.de
Massimo Barra Sales Iserlohn
Tel.: +49 (0)2371 - 2105 - 43
E-Mail: barra@marx-gmbh.de
Klaus Mayer Sales Donauwörth
Tel.: +49 (0)906 - 127977 - 55
E-Mail: mayer@marx-gmbh.de
Crucible induction furnaces
The requirements for modern crucible furnace systems, especially regarding power density, availability and operational safety, have increased significantly in recent years. Our decades of experience in the field of coil repair and modernization of crucible furnace systems are of great importance here.
The design, construction and implementation of the new production, modernization and repair of crucible furnace systems are carried out in close cooperation with the customer in order to develop optimal solutions for your applications.
New crucible furnace coils (use under vacuum or normal atmosphere) can be manufactured with a diameter of up to 2200mm. The MARX insulation technology including the saturating process offers the greatest possible protection for your coils.
Due to the high proportion of in-house production (coils, magnetic yokes, steel construction,...) we can react immediately in order to repair your systems as quickly as possible.
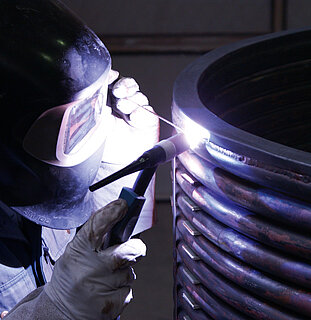
- New production
- Coil repair of all brands
- Volume increase
- Increase in performance
- Coil optimization
- Water-cooled coil compensation
- Coil lining
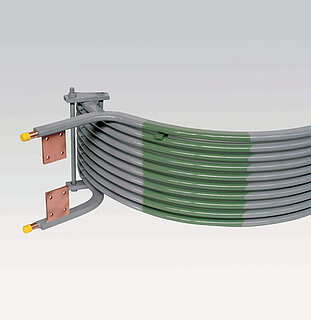
- 3-fold plastic coating of the copper profile using Heat-resistant special plastic material
- Intermediate insulation made of special mecanite or GHG (Glass fabric)
- Complete impregnation with electrical insulating varnish (Grade H) (also under vacuum)
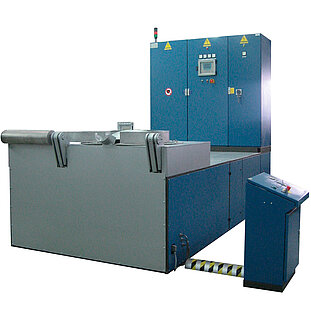
- Alloy: Iron and non-ferrous metals
- Power unit: MF (transistor technology/IGBT)
- Capacity: up to 3t
Our compact furnaces and small crucible furnace systems stand out for their compact design with a capacity of up to 3 tons. They are designed for iron, steel or copper and their alloys. The smallest crucible furnace built by MARX to date has a capacity of 6kg of aluminium.
Details
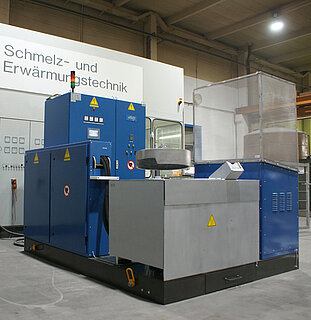
Alloy: iron and non-ferrous metals
Power unit: MF (transistor technology)
Capacity: 80 kg
- Furnace for sampling and alloying tests
- Furnace power: 100kW
- Mains connection: 3x 400V ± 10%, 50Hz
- Melting capacity: about 40min / 80kg
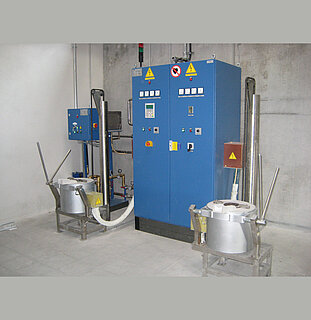
Alloy: aluminum
Power unit: MF (transistor technology)
Capacity: 6 kg
- for trial melting of aluminum alloys
- IGBT transistor converter with 2x20kW
- including water cooling system
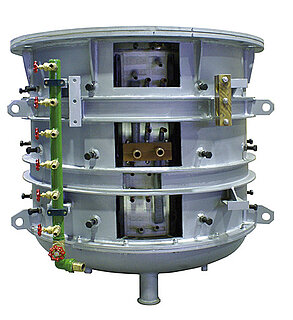
Power: 100 to 1,000 kW
Alloy: non-ferrous metals (Al / Cu)
Power unit: NF / MF
- Inverter in transistor technology IGBT
- Compact design with prefabricated crucibles
Channel induction furnaces
The channel furnace technology developed by MARX aims to make intensive use of the advantages of modern channel furnace systems, their special energy efficiency and the wide range of possible uses and applications.
In order to meet the high requirements of energy saving, maximum melting capacity and service life, the MARX channel inductors were developed with geometrically adapted channels. This type of technology enables a significant increase in service life while at the same time reducing energy consumption.
For example, channel inductors with an output of up to 2,400 kW for copper alloys and 1,500 kW for aluminum were developed and tested. The power supply can either be supplied conventionally or using IGBT converter technology.
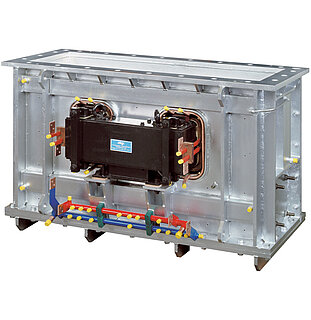
Inductor power: 60 to 1,500kW
- Melting furnaces
- Holding/Storage furnaces
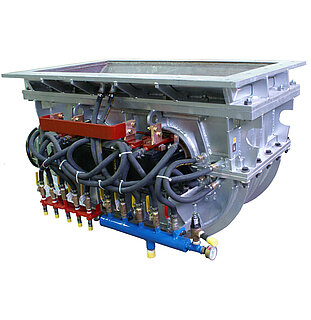
Inductor power: 50 to 2,500kW
- Melting furnaces
- Holding furnaces
- Combined melting and casting furnaces
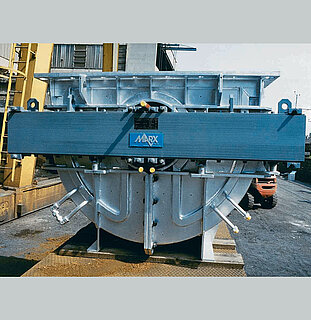
Inductor power: 125 to 2,000kW
- Storage Furnaces
- Dosing Furnaces with forehearth and pouring plug device
- Version with water-cooled housing and water-cooled transformer
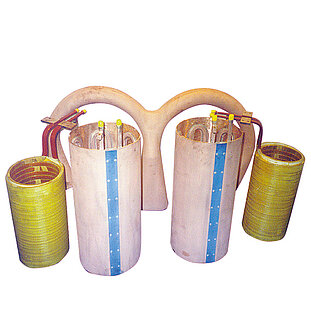
- Spare coils
- Cooling cylinders
- Channel formers
- High-current cables (water-cooled)
- Capacitors
- Balancing chokes
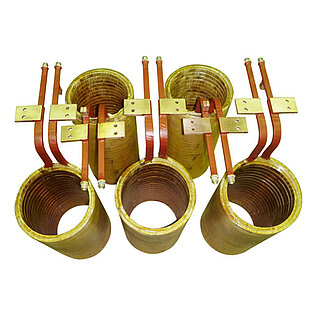
- in the water-cooled system (WF)
- in the air-cooled system (AF)
- Thermal insulation class H (to withstand +180°C continuously)
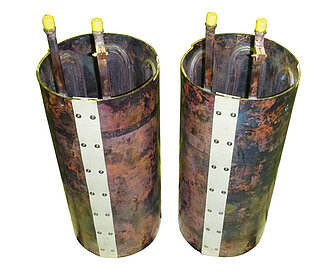
- Made of copper for water-cooled system (WF)
- Made of stainless steel for air-cooled system (AF)
- Made of stainless steel for water-cooled system (WF)
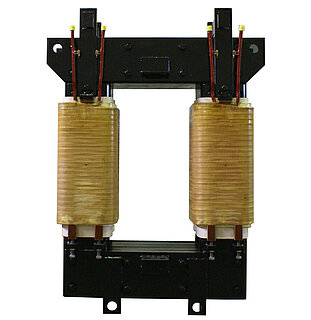
- Made of high-quality grain-orientated transformer laminations
- Insulated and bolted together with solid clamping plates
- Provided with a yoke that can be removed at one end
- Design: 2, 3 or 4 legs
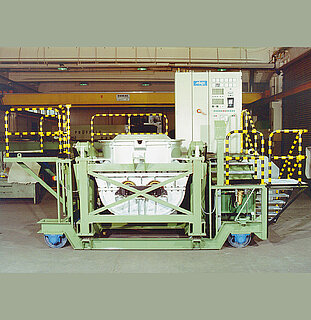
Capacity: 1,000 kg (Cu)
Type: MNFR-Cu-1,000 / 340
Rated power: 250 kW / 340 kW
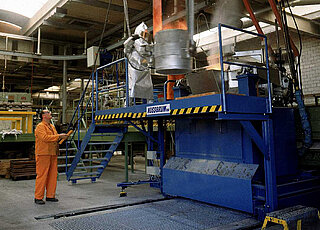
Capacity: 1,6t (Cu)
Type: MNFG-Cu-1.600/240
Rated power: 240kW
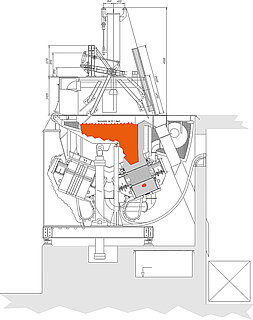
Capacity: 32t (Ms)
Type: MNFR-25.000-Ms-4.800kW
Rated power: 4.800kW
Melt rate: approx. 20t/h
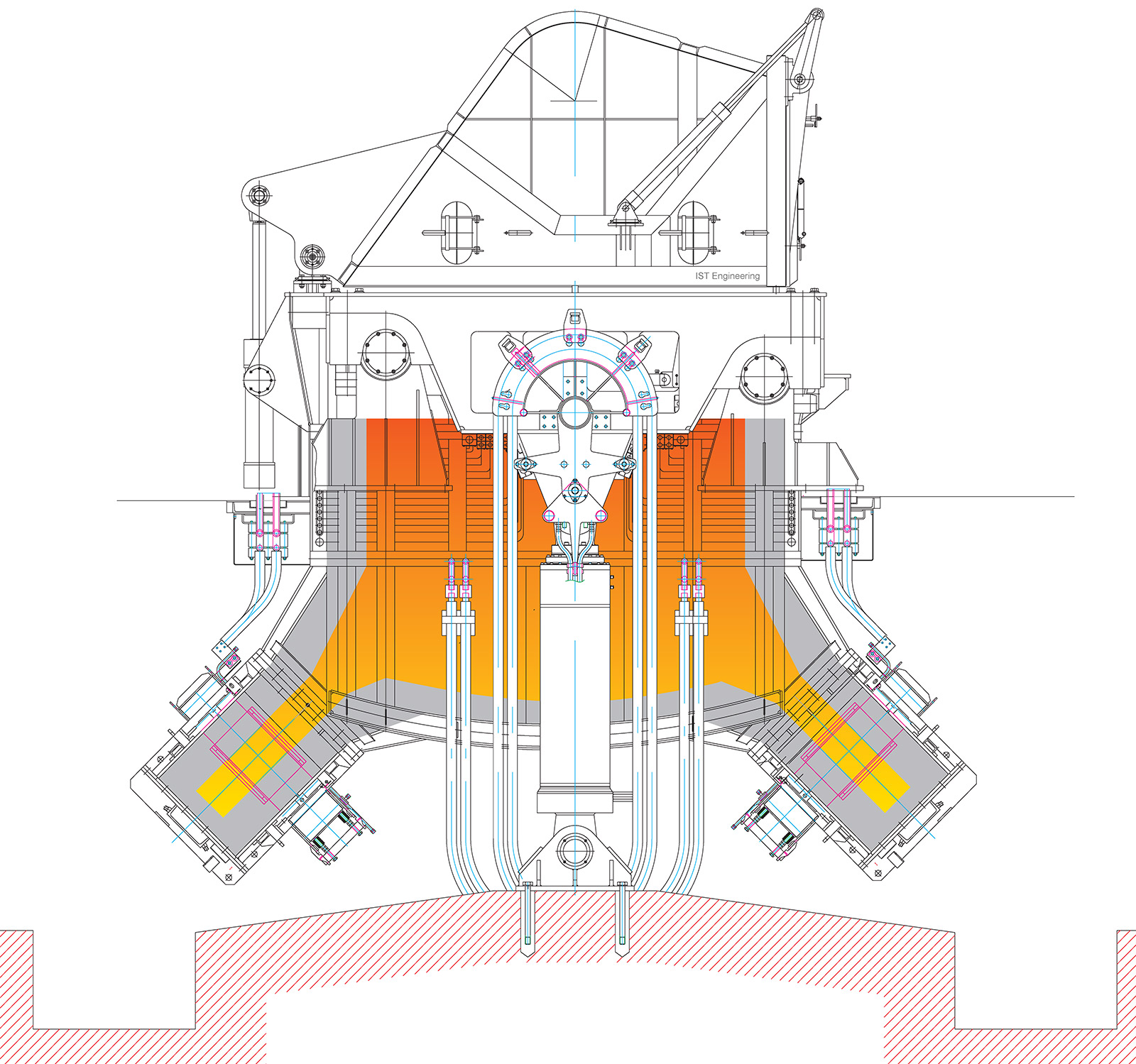
Capacity: 70t Aluminium
Effective load: 52t Aluminium
Rated power: 6,000 kW
Modernisation & conversion
What should a foundry do that is equipped with systems from the 1960s and 1970s and needs a foundry at the level of modern technology and efficient production processes in order to survive on the market? Whoever has the investment funds builds a new foundry. If you do not have them, or only have them in part, or if you have to set different priorities, you will have a look at your old systems and carry out a program for technological upgrading and increasing efficiency.
Old melting plants hold great potential for reusable plant parts and technologies that can be used. Current requirements for efficiency, energy saving, environmental friendliness and safety can also be met with existing systems in most applications.
The replacement of individual components such as the power section, control or cooling will bring your existing system up to the current state of the art and thus offer similar advantages to a new system. For example, by upgrading to the latest IGBT converter technology, almost maintenance-free operation of the power unit can be ensured.
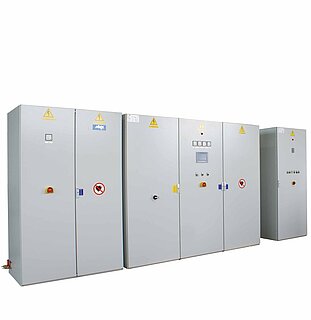
- Balanced load on the mains power supply
- Infinitely variable power feed
- Power factor (cos phi) close to 1
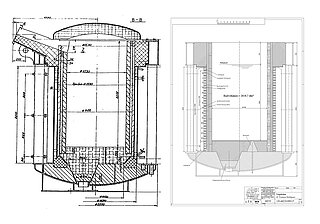
Old melting plants have great potential for performance improvements. A wide range of reusable plant parts and technologies can easily be utilised in order to exploit this potential.
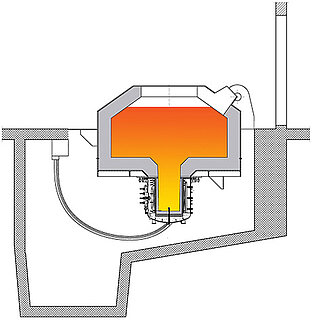
Coreless induction technology replaces channel inductor technology for slag forming aluminum-alloys with the advantages:
- longer lifetimes
- no cleaning cycles
- no production downtimes due to cleaning
Service & maintenance
Customer service is our top priority. Fast response times and flexibility are essential nowadays. We therefore offer you the opportunity to contact us at any time via our 24-hour emergency number!
With a total of three production and service locations in Germany, we are able to reach and support our customers throughout Europe as quickly as possible. Our assembly staff also has many years of experience and is thus able to provide solutions competently, reliably and quickly.

- Individual, personal specialist advice on site
- Detailed offer preparation for full service and cost transparency
- Elaboration of customer-specific solutions
- Comprehensive spare parts service
- 24-hour availability via our service emergency number
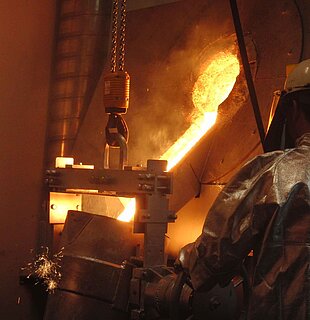
- Commissioning, at customer request also at night and on weekends to avoid downtimes
- Oven inspections and preventive maintenance
- On-site troubleshooting
- Training and instruction of the specialist and operating personnel on site
- Maintenance seminars for induction furnaces
- Safety seminars induction furnaces
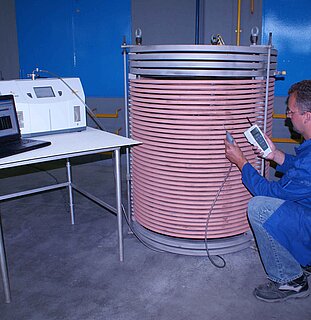
- Water flow test
- Water pressure test
- Endoscopic examination
- Helium leak rate test
- Insulation measurement
- Electrical tests according to EN standards
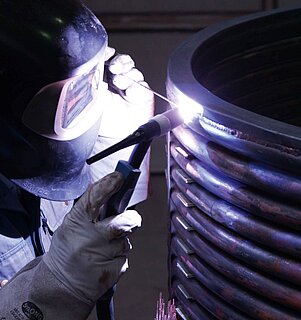
- Coil repairs of all brands
- On-site emergency repairs
- Repair of magnetic yokes
- Coil change of all brands on site
- Coil storage
- Fast spare parts service