EXTRUSION HEATING SYSTEMS
The company Marx GmbH & Co. KG in Iserlohn has been involved in heating extrusion billet containers since the 1960s. The development began back then with tests on external heaters and internal induction heaters, which have now been largely replaced by modern resistance heaters.
The heaters have become increasingly intelligent over the years, which is why our heating design has been given the name "MARX Smart Containers". This name has established itself on the market and has been associated with high quality and durability since then.
Ahmed Sbai Sales Iserlohn
Phone: +49 (0)2371 - 2105 - 56
Email: Sbai@marx-gmbh.de
Moritz Boss Sales Iserlohn
Phone: +49 (0)2371 - 2105 - 32
Email: boss@marx-gmbh.de
Smart Container TM
In addition to the development of improved steel qualities and the geometric design of containers, improved heating and cooling are essential tools for modern extrusion technology. The coordination of these service providers is critical to production and quality just as these components influence the life of the containers as press tools.
The modern billet container heaters can be heated in different areas thanks to an intelligent and differential value regulating control. Additionally, in many cases a sectional cooling is introduced into the billet containers, which is also regulated by the software control, with the aim of achieving a controlled and constant temperature behaviour, to support isothermal extrusion.
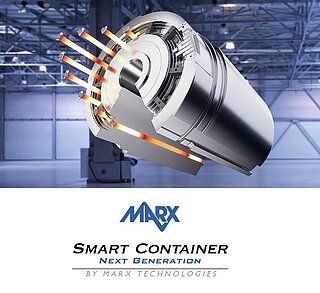
The next generation of Smart Containers is based on 3-zone cartridges, which offer the optimal conditions to react flexibly to the different requirements of the production process. "Zone 1" and "Zone 3" are short, powerful zones that allow optimal temperature control during production both on the tool side and on the stem side. The middle "Zone 2" is longer and designed with less power in order to be able to switch off the heating in the warmest area in the middle of the container over a large area during production.
Details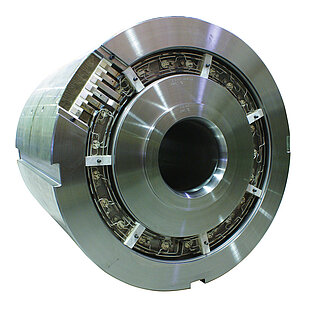
The current state of development of the process-controlled “Smart Containers” means that they can be heated up and regulated at weights of between 500kg and over 100 tons in segmented heating zones.
The high-power heating cartridges can be produced with up to three heating zones and achieve a proven service life of up to 5 years and above depending on their intended purpose.
Details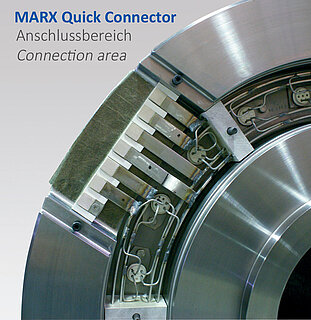
No matter whether frequent container changes or longer production periods - we have the right connection system for you!
Choose between our quick connection "MARX Quick Connector" and the compact connection "MARX Compact Connector".
Details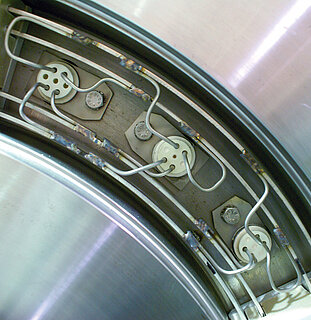
The welded design of the cartridge heater offers all the advantages of a modern heating system for containers in extrusion presses.
It guarantees the highest possible security for permanent fixed connections and enables a simple, clear and therefore repair-friendly construction of the heating.
Details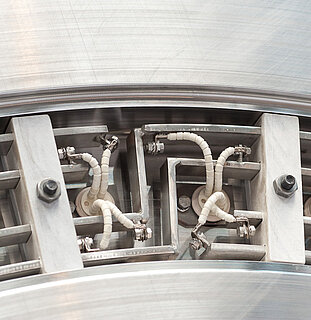
The MARX screw connection for easy self-assembly.
In addition to the advantage that the cartridges can be installed or replaced with simple tools, there are hardly any other advantages over the welded variant.
DetailsTool heating systems
The temperature of the tool is often the decisive success factor for complicated press profiles. If the temperature is not correct here or changes during the pressing process, this affects the quality of the profile and often leads to rejects.
The reason for a too low temperature is often the relatively cold die holder, which extracts the heat energy from the precisely preheated tool. To prevent heat flow, MARX has developed special tool holder heating systems that prevent the heat from flowing quickly from the die to the holder.
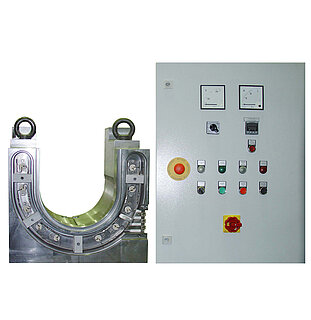
Low temperatures of the die carrier are often a reason for quality problems. The cold die carrier absorbs the thermal energy from the precisely preheated tool and thus has a negative impact on the pressing process.
The die slide heating from MARX prevents the heat from flowing quickly from the die to the holder.
Details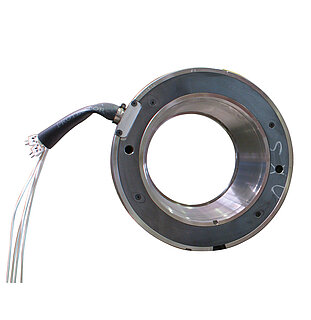
Especially with small, filigree profiles, such as the MMP (Micro Multi Ports) products, the exact temperature control during the pressing process is extremely important.
The MARX die-holder heater was developed for these special applications and prevents the temperature from flowing away towards the die-holder.
Details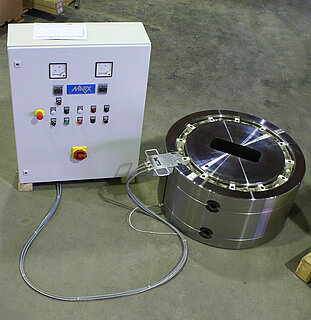
With the help of our special bolster heater, you can easily heat the bolster in the press.
The installation principle and the arrangement of the heating elements are based on our proven container heating.
Details
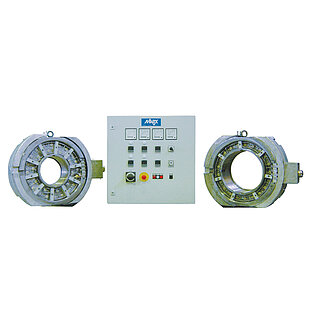
For special applications, in addition to extrusion, customized solutions for heating various components are often required. MARX also offers individual special solutions in this field.
An example of such an application is the forging press tool heater for forging aluminum with the aim of "isothermal forging".
DetailsTool stations & Preheating stations
In order to meet today‘s modern demands, special tool stations have been developed at MARX, to heat up the extrusion press tools to an optimal process temperature.
The container preheating stations are either fitted with independent heating systems, or can be operated via the resistance heating system integrated in the container. In this case, power is supplied automatically via a pneumatic contact unit. The heating process is precisely controlled via integrated controllers.
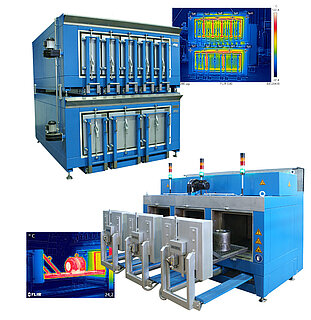
The "Smart Heat" range of die ovens from Marx have been specially constructed for the preheating of extrusion dies.
They have one or more furnace chambers, which are heated according to the "recirculating air principle" and thus guarantee an even temperature distribution in each chamber.
Details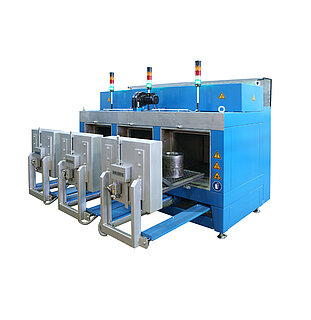
Marx die oven with 3 drawers for extrusion dies with a weight of up to 250kg.
Inner dimensions per furnace chamber: 670x525x500mm (LxWxH)
Max. Weight per furnace chamber: 250 kg
Rated power: 42 kW
Nominal temperature: 480°C
Details
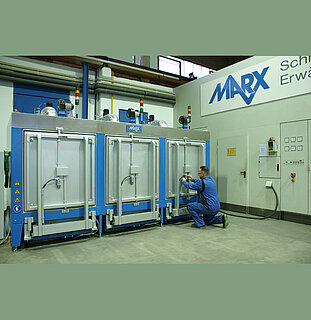
Marx die oven with 3 drawers for extrusion dies with a weight of up to 880kg.
Inner dimensions per furnace chamber: 1000x1000x1000mm (LxWxH)
Max. Weight per furnace chamber: 880 kg
Rated power: 72 kW
Nominal temperature: 480°C
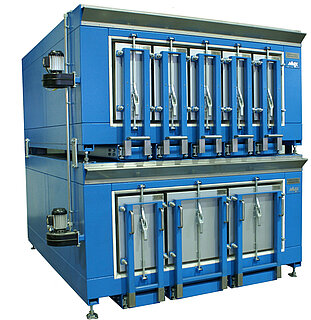
Marx die and mandrel oven with 8 drawers for extrusion dies and mandrels.
Inner dimensions per furnace chamber: 1500x400x1500mm (LxWxH)
Max. Weight per furnace chamber: 220/140kg
Rated power: 54kW
Nominal temperature: 350°C
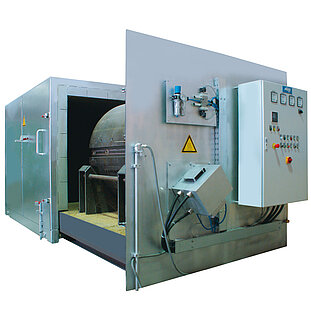
The container preheating stations are either equipped with their own heating or can be operated using the resistance heating integrated in the container itself.
The heating process is precisely controlled by an integrated control.
DetailsService & maintenance
Customer service is of top priority for us. Fast response times and flexibility are vitally important these days. That‘s why we make it possible for you to contact us at any time on our 24h emergency number. With a total of three production and service sites in Germany, we can reach and support our customers all over Europe as quickly as possible.
Our assembly personnel also have years of experience, enabling them to provide solutions competently, reliably and quickly.
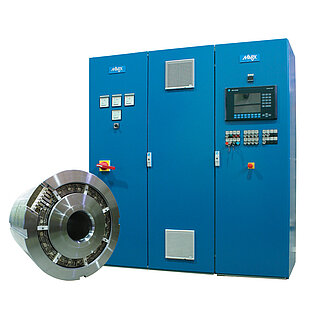
Old container heating systems no longer meet today's requirements of modern production processes. These are often inflexible and energy intensive.
Retrofitting and modernizing old heating systems are often relatively easy to implement and offer great potential for energy savings.
Details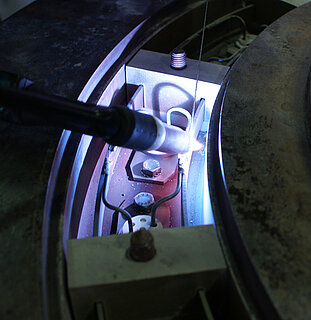
Container heating systems of various brands can be checked, repaired and serviced in-house.
The individual components for connection, insulation and temperature measurement are individually designed, constructed and manufactured for the respective container.
Details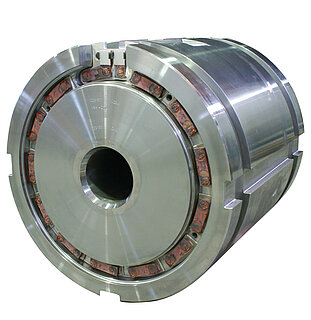
New production and repair of induction heating as a replacement in extrusion containers of all press sizes existing worldwide.
Internal heating connections in welded and soldered version, soldered version also with nickel plated heater rods and interconnection bars. Power-contacts with
silver-plates.
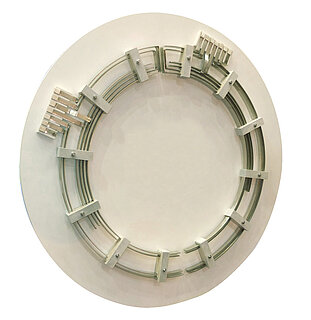
Our ready-to-install installation kit enables the resistance heater to be fitted precisely, quickly and easily on site.
With the help of the pre-assembled heater, the installation time into the container is significantly reduced and can usually be carried out by the customer's own electrician.
Details