FOUNDRY-LADLES
Our delivery program includes pouring, transport and treatment pans, the dimensions of which correspond to customer requirements. As a certified welding company according to DIN EN ISO 3834-2, we are able to offer our casting ladles from our own production, in accordance with the high requirements of the product standard DIN EN 1247. In addition, we have our specially designed "MX" gearbox series, which we also manufacture in-house.
NEWS: Our new battery drive is now available! After the introduction of our new battery drive technology in 2019, a lot of practical experience could be gained both on new and on retrofitted ladles. Find out more about the advantages here!
Dirk Kirchhoff Sales Iserlohn
Phone: +49 (0)2371 - 2105 - 28
E-Mail: kirchhoff@marx-gmbh.de
Oguz Cetiner Sales international
Phone: +49 (0)2371 - 2105 - 48
Email: cetiner@marx-gmbh.de
Adrian Sturm Sales Donauwörth
Phone: +49 (0)906 - 127997 - 56
Email: sturm@marx-gmbh.de
Kerstin Krökel Sales Hennigsdorf
Phone: +49 (0)3302 - 2009 - 30
Email: kroekel@marx-gmbh.de
Crane foundry ladles
MARX offers a range of services from a single source, starting with new construction, through the repair and overhaul of pouring ladles and gears, to pouring ladle inspections in accordance with UVV as well as training courses on occupational safety and testing of pouring ladles.
As your partner in security issues, we carry out the annual visual inspection for you. The main tests are carried out, depending on the customer's requirements, in our factory or directly on site by one of our specialists.
Treatment ladles
A treatment ladle is basically a crane pouring ladle, which usually has a mounting device for a crane or forklift. The difference to the usual ladle is essentially the vessel geometry and, if necessary, the choice of material. The vessel height in relation to the diameter has a size ratio of approximately 2:1. The diameter is smaller in order to keep the oxygen uptake of the melt via the bath surface as low as possible.
MARX standard ladles
MARX offers you a selection of standard ladles.There is a selection of a total of five different sizes, from 1t to 10t capacity. They are driven by our proven MX ladle gearboxes for smooth and safe handling of the ladles.
With the MARX standard ladles, we are able to offer pre-configured foundry ladles at especially reasonable prices.
The design we selected based on a modular design principle allows a reduction of the procurement costs while maintaining our high quality standards. Our production facilities within the MARX Group allow us to offer complete foundry ladle production from a single source. In this way we guarantee the highest quality through reliable processing for a long service life.
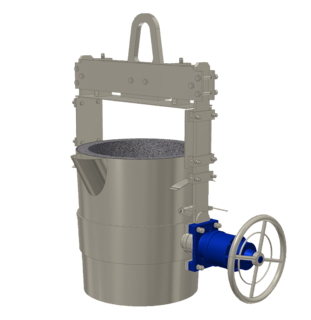
Capacity: 1t (Fe)
Dimensions: 55‘’x61’’ (WxH); 1,400x1,550mm
Weight: 350kg (without lining)
Gearbox: MX-1 60V
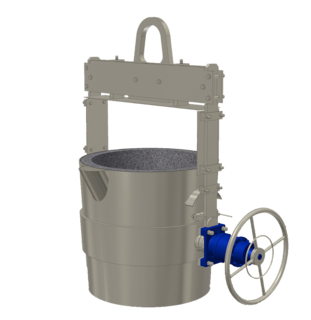
Capacity: 2t (Fe)
Dimensions: 63‘’x73’’ (WxH); 1,600x1,850mm
Weight: 580kg (without lining)
Gearbox: MX-1 60V
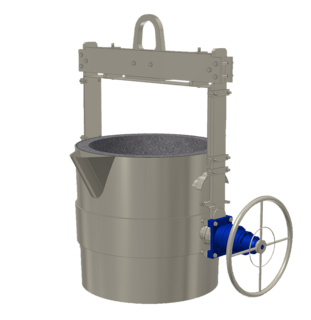
Capacity: 5t (Fe)
Dimensions: 83‘’x93’’ (WxH); 2,100x2,350mm
Weight: 1.3t (without lining)
Gearbox: MX-2 80V
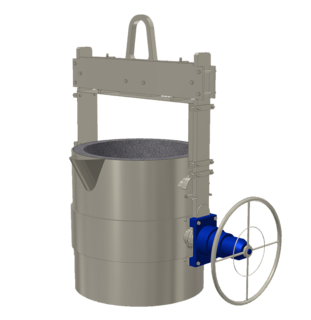
Capacity: 7t (Fe)
Dimensions: 93‘’x108’’ (WxH); 2,350x2,750mm
Weight: 2.2t (without lining)
Gearbox: MX-3 110V
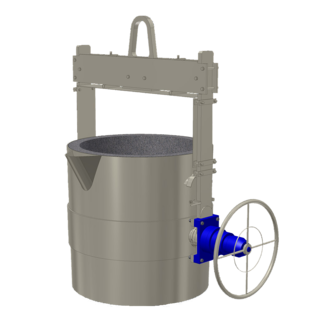
Capacity: 10t (Fe)
Dimensions: 100‘’x118’’ (WxH); 2,550x3,000mm
Weight: 2.6t (without lining)
Gearbox: MX-3 110V
Ladles - special applications
Our ladles are manufactured individually according to customer requirements. Special solutions for special requirements are therefore part of our daily business. So that you can get an idea of these special designs, here are some examples of special pouring ladles:
Siphon ladles, stopper ladles, drum ladles, forklift ladles, ladles for automatic pouring devices, hand pouring ladles, ladles with lid device, ladles with exchangeable lifting device (C-hanger, prism holders, hooks, ...)
No matter what solution you are looking for, we will be happy to advise you. Contact us.
Gear and drive technology
Our MX series gearboxes are characterized by a particularly robust design. Certified by Germanischer Lloyd, they offer the highest level of security.
All gearboxes are equipped with a brake that acts automatically in both tilting directions and holds the ladle in any desired tilting angle, thus ensuring the necessary self-locking. When developing the specially assembled gearboxes, great value was placed on components from regional suppliers, such as for the cast parts or the machining work.
Various auxiliary drives are available for the MX gearbox.
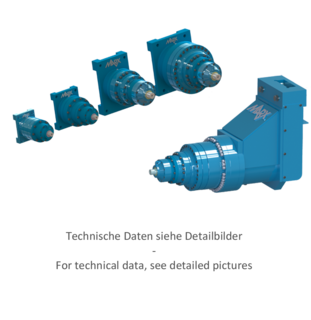
Our MX planetary oil bath gearboxes have been specially developed for use on foundry ladles.
They are compatible with a large number of ladles in use with a capacity of 0.3t to 50t.
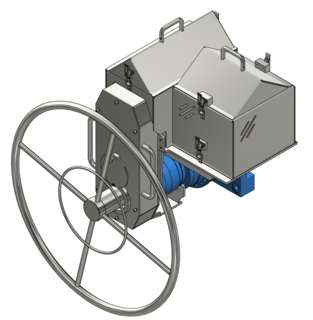
Our battery drive for independent work!
No supply lines are required, as is the case with conventional electrical or pneumatic auxiliary drives. This enables flexible use at all locations in the foundry that can be reached with the ladle.
Details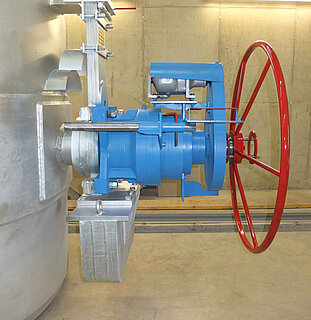
Our module-based gearbox series enables quick and uncomplicated retrofitting of a pneumatic tilt drive instead of the handwheel.
Details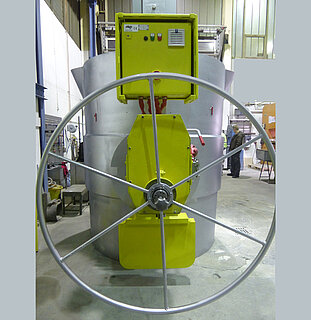
In special cases, the application requires the ladle to be operated using an electric drive. When it comes to electric geared motors, MARX relies exclusively on renowned suppliers.
Details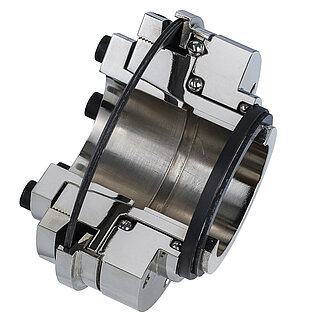
To prevent overload damage to the gearbox from auxiliary drives, MARX uses safety clutches that limit the input torque to the maximum value permitted for the gearbox.
Details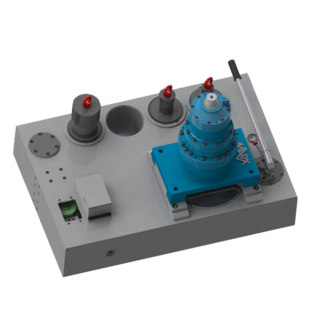
Since the introduction of the updated DIN EN 1247 in December 2010, a review of the output as well as the brake torque is required every two years.
Details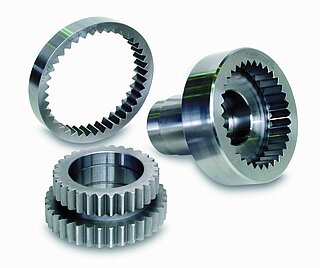
Based on our experience over many years, we are in a position to offer a comprehensive range of spare parts and maintenance services for all the popular planetary oil bath gearboxes and eccentric gears.
DetailsWire-treatment
The MARX DIM systems are specially designed for treating and inoculating gray cast iron. The treatment process is precisely adjusted to the individual melt treatments and can be called up fully automatically.
The treatment cabins can be fitted with special, designated treatment ladles and can also be adapted to the customer‘s existing ladles.
The ladles are positioned in the cabin with a carriage car or directly with the forklift. Depending on the selection, the cabin is closed either with the carriage car or, alternatively, with a bulkhead. To ensure complete exhaust of emissions, they are extracted from both the ladle cover and the cabin.
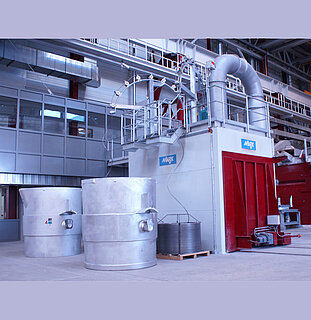
Treatment Station for gray iron
Ladle capacity: 18t, 21t and 40t
Injection speed: up to 60m / min
Wire diameter: 5mm to 20mm
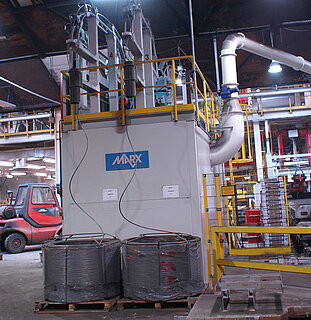
Treatment Station for gray iron
Ladle capacity: 2.6 to 3.5t
Speed of injection: up to 60m/min
Wire diameter: 5mm to 20mm
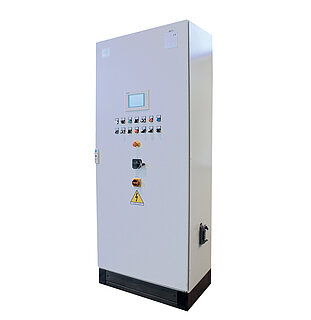
The installation can be operated with a touch-panel in the control cabinet, for example.
Details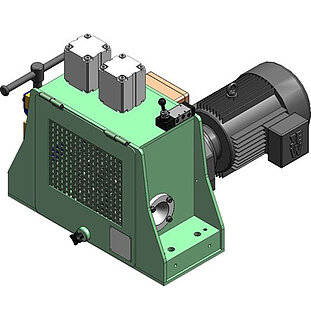
The treatment stations can be equipped with multiple wire feeding machines that operate simultaneously.
DetailsService and maintenance
Customer service is of top priority for us. Fast response times and flexibility are vitally important these days. That‘s why we make it possible for you to contact us at any time on our 24h emergency number. With a total of three production and service sites in Germany, we can reach and support our customers all over Europe as quickly as possible.
Our assembly personnel also have years of experience, enabling them to provide solutions competently, reliably and quickly.
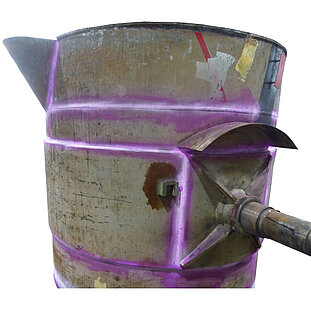
We take care of the inspection and repair of your crane ladles considering the current regulations, such as DIN EN 1247 and DGUV.
Depending on customer requirements, the main tests are carried out at our factory or at the customer. With the help of our mobile gearbox test rigs, we are able to test the required output and braking torques of the gearboxes on site.
Details
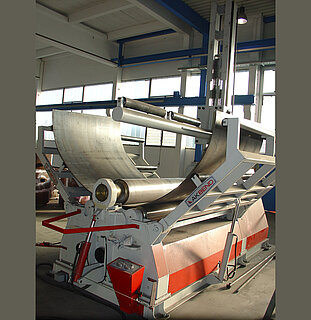
When it comes to quick and reliable repair or maintenance of ladles and gears, you have chosen the right partner with MARX.
With our own production facilities at all locations in Germany, we can offer quick and flexible problem solutions so that your ladles are available for production again as quickly as possible.
Details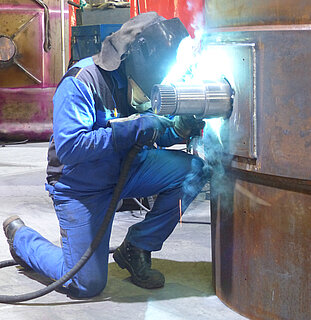
Old ladles can be converted in many cases to meet today's safety standards.
Especially for large ladles over 15t it can be worthwhile to consider retrofitting or converting. Retrofitting additional drives is also possible in many cases.
Details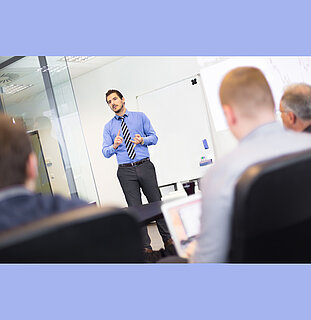
Together with the TÜV Rheinland (German technical inspection authority), we offer training seminars on the topic »Testing of foundry ladles« (German language).
After a successful completion of the training »Competency for the Inspection of Casting Ladles«, every participant receives a TÜV certificate.
Details